Alfa Romeo M32 Gearbox Repair | Clutch & Flywheel Replacement | Eco Torque Ltd
- Eco Torque
- Jan 24, 2017
- 2 min read
Updated: Apr 13, 2022
In this blog we have an Alfa Romeo 159 in for the M32 6 speed gearbox bearing replacement as well as a new clutch and dual mass flywheel. This vehicle had age related wear to the clutch and dual mass flywheel. More information www.eco-torque.co.uk or email info@eco-torque.co.uk.
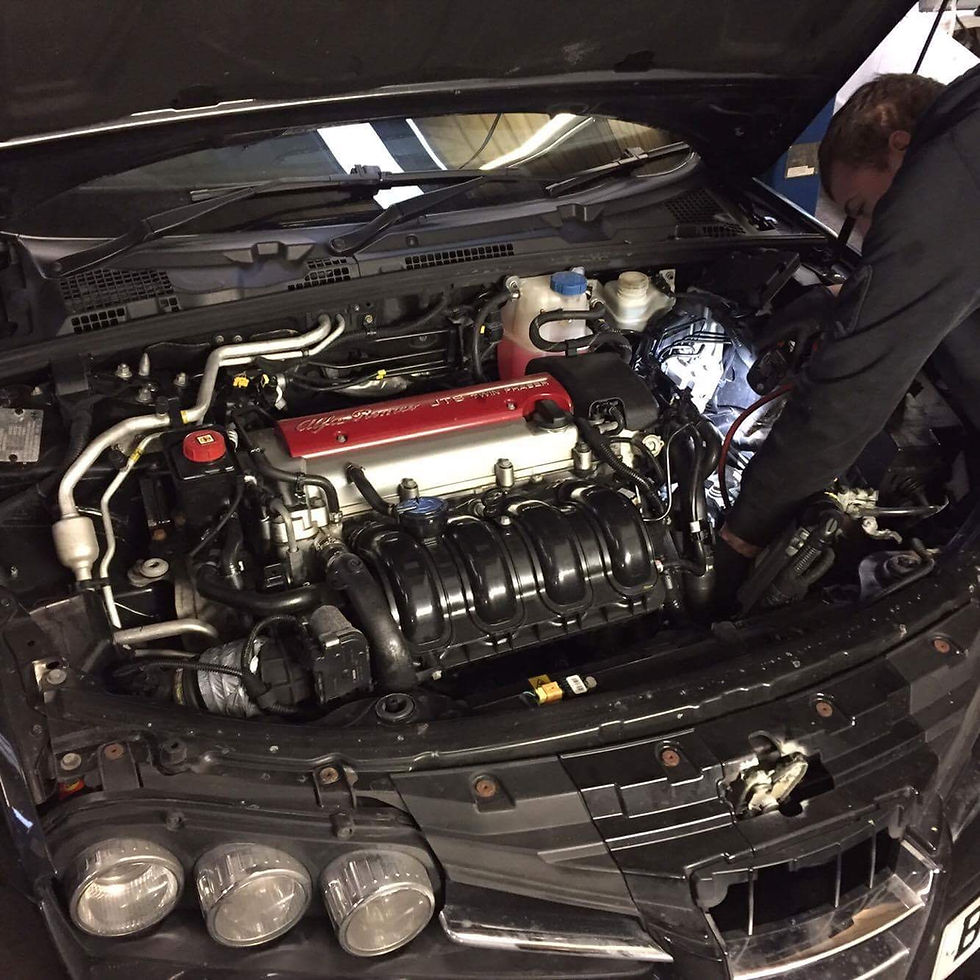
As engine bays go, this is certainly one of the prettier ones that we see. As most modern vehicle engines are covered by large bulky plastic covers to hide the pipes and ancillaries, this care shows them off.
This particular car was showing the common wear symptoms of the M32 transmission as well as other issues. As a matter of precaution the customer wished to change the DMF and clutch system.
The sub-frame on the vehicle had started to rust in various places, which always causes issues when trying to remove connecting bolts and fixings. This caused a severe problem with two large M14 chassis bolts on the drivers side. They secured through the subframe into the chassis via to rivets. These rivets had rusted and completely detached resulting in the bolts simply spinning and not being able to be removed. Both bolts had to be cut and replaced with new ones from Alfa Romeo.
After battling the rust and finally removing the gearbox we could see a fair amount of play in the dual mass flywheel as well as fatigue on the friction surface of the clutch plate.
Both dual mass flywheel, securing bolts and complete three piece clutch system were replaced with LUK products. As mentioned in many of our blogs we always try to use LUK parts were possible due to the superior build quality.
No external damage to the gearbox housing and no visible leaks on inspection.
Small and fine metal deposits like this are normally a good indication that there will be wear or pitting on the bearings in the M32. Some of this will also be metal that is worn off the inner teeth of the gear upon bad gear selection or failing synchromesh's. 3rd and 4th gear being the most common to suffer from this issue.
As you can see from the picture below the 6th gear end bearing has a distinctive wear pattern on it. These wear patterns will be present on the other bearings inside the box as this issue takes its toll on the whole unit.
The normal procedure in this scenario is to replace all bearings with new parts as well as hot wash components and wet blast the casings ensuring a complete clean.
This customer had the updated end casing and larger end bearings fitted to stop and future issues that could result in failure. Please look at our other blog entries here for more information on this upgrade.
As you can see there is a clear difference between the reconditioned gearbox and the surrounding bodywork. From this image you can also see on the right hand side the heavy surface rust forming on the sub frame of the car.
After a test drive and final check the vehicle was handed back to the customer.
Please Like & Share
01462 835335
Comments